The world of electronics manufacturing is ever-evolving, with the quest for perfection driving innovation at every turn. At the heart of this quest lies one seemingly modest yet pivotal component: solder wire. Not just any solder wire, but high purity solder wire, which has emerged as a linchpin in the assembly of reliable, high-performance electronic devices. Understanding the essence, benefits, and practical implications of using high purity solder wire can illuminate why it's considered a superior choice for electronic projects.
The Essence of High Purity Solder Wire
High purity solder wire is characterized by its minimal impurity content. Unlike standard solder wire, which may contain a mix of metals and other elements that could compromise its performance, high purity solder is refined to remove as many impurities as possible. This meticulous process ensures that the solder offers superior characteristics essential for high-quality electronic assemblies, such as enhanced electrical and thermal conductivity.
Why High Purity Matters in Electronics
In the realm of electronic assemblies, the role of solder wire extends beyond merely joining components; it's crucial for ensuring the integrity and reliability of every connection. Impurities within solder can significantly impact its performance by reducing its conductivity, creating voids in solder joints, and ultimately compromising the strength and reliability of these connections. High purity solder wire, with its reduced impurity content, mitigates these risks, thereby enhancing the overall performance and longevity of electronic devices.
Advantages of Using High Purity Solder Wire
Employing high purity solder wire in electronic manufacturing offers several compelling advantages. Its enhanced electrical conductivity ensures efficient signal transmission between components, a critical factor in the functionality of any electronic device. Improved thermal conductivity facilitates better heat distribution during soldering, reducing the risk of heat damage to sensitive components. Moreover, high purity solder tends to produce fewer voids in solder joints, a common issue that can lead to joint failure under stress. The result is increased joint strength and reliability, critical factors in the longevity and durability of electronic devices.
Practical Implications for Electronic Device Manufacturing
Case studies and testimonials from industry professionals underscore the difference high purity solder wire makes in device longevity and performance. For instance, the Truden Tool by Kaina Tin, a 900g high purity no-wash active solder wire, exemplifies the advancements in solder wire technology. Its high brightness and C1 tin composition underscore its superior quality, making it a preferred choice for manufacturers seeking to enhance their product's reliability and performance.
Choosing the Right High Purity Solder Wire for Your Project
When selecting a high purity solder wire, various factors must be considered, including composition, diameter, and whether a flux core is necessary for your specific application. Products like the Kaina Tin high purity solder wire, characterized by its no-wash active formulation, offer convenience and efficiency, making them ideal for a wide range of soldering tasks.
Working with High Purity Solder Wire: Best Practices
To achieve optimal results when using high purity solder wire, certain best practices should be followed. Proper preparation and handling are essential to prevent contamination, while employing the right soldering techniques can enhance the quality of solder joints, ensuring the durability and reliability of the finished electronic device.
Exploring the Environmental Impact
The manufacturing and disposal processes of high purity solder wire also present a lesser environmental impact compared to their lower purity counterparts. With a focus on waste reduction and recycling, high purity solder materials are not only beneficial for electronic device performance but also for promoting sustainability in the electronics manufacturing industry.
Future Trends in Solder Wire Technology
Innovations in purity and manufacturing processes continue to push the boundaries of what is possible with solder wire technology. The drive towards even higher purity levels, coupled with advancements in how solder wire is produced, promises to unlock new applications in electronics, further enhancing device performance and reliability.
Final Thoughts: The Value of Investment in High Purity Solder Wire
The myriad benefits of high purity solder wire, from enhanced electrical and thermal conductivity to increased joint strength and environmental sustainability, underscore its value in electronics manufacturing. As the industry continues to evolve, the importance of investing in high-quality materials like high purity solder wire becomes increasingly clear. For those looking to elevate the performance and reliability of their electronic devices, considering a high purity solder, such as the Kaina Tin high purity no-wash active solder wire, is a step in the right direction.
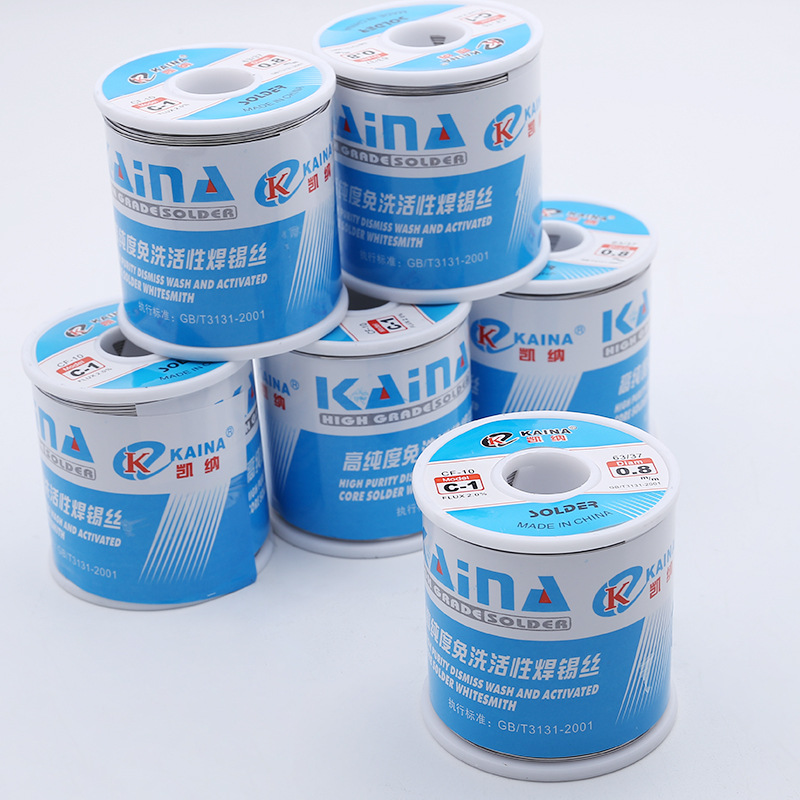